When it comes to workplace health and safety, risk management involves identifying potential hazards, assessing the risks of those hazards and putting appropriate control measures in place to eliminate or reduce the risks. The work doesn’t stop there however. After control measures have been implemented, every workplace has an obligation to do their best to make sure they remain effective and to review them on an ongoing basis.
Especially as some of us are returning to work and adjusting to a post-COVID world, it’s important that any control measures that have been implemented pre- and post-pandemic are being reviewed and remain effective.
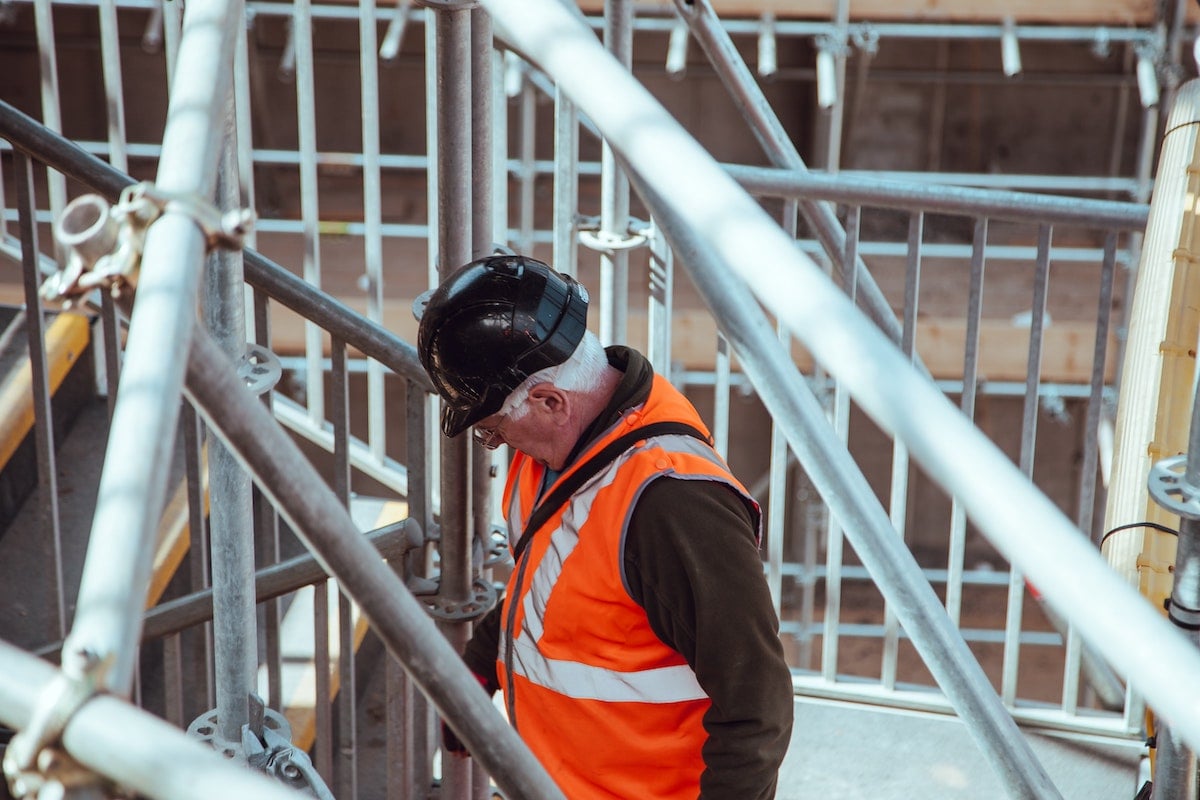
Reviewing Your Control Measures
There are two main components to consider when reviewing your control measures. First, when will you be reviewing them. Managing workplace health and safety is an ongoing process, so your organisation should be reviewing your control measures regularly. Instead of relying on the assumption reviews will happen on an ongoing basis naturally, a schedule should set for when the reviews will happen. How frequently these reviews are scheduled depends on the nature of your organisation. For example, if your company deals with numerous high risks, your control measures should be reviewed more frequently. By having a schedule, you will ensure that your control measures are examined even if they seem to be working fine.
In addition to a schedule, your organisation's work health and safety plan should include triggers that indicate when a review is required. By having these outlined, it will ensure that measures are reviewed in advance of your schedule if necessary. According to Safe Work Australia, a review is required:
- When a control measure is not effective in controlling a risk
- When a change is being made at the workplace that an existing control measure may not be fit to manage
- If a new hazard or risk is identified
- If a consultation indicates a review is necessary
- If a HSR requests a review
The second component to consider is your approach in reviewing the control measures. Essentially you should follow the same steps you take to identify hazards at the beginning of your risk management process. This involves consulting with the workers who are most close to the risk being controlled and working together to address the following:
- Are control measures working effectively in design and operation?
- Are the frequency and severity of health and safety incidents reducing over time?
- Have the control measures created any new problems?
- Have any new equipment or materials been introduced that could affect the effectiveness of the control measure?
- Has any new legislation been introduced that could impact the effectiveness of current control measures?
- Are procedures being followed properly and is employee training up-to-date?
By asking these questions, if there are any issues that come to light with the effectiveness of the control measures, your Health and Safety Representatives and workers can consult to make decisions on what improvements need to be made.
Ensuring your control measures remain effective
Establishing a cadence for control measure checks is one way to ensure your control measures are working as planned. In addition, there are other steps you can take to make sure the effectiveness of your control measures is maintained and they can withstand any changes in operating conditions.
1. Assign accountability
All workers are responsible for being conscientiousness of workplace health and safety, but it's important to establish to accountability among various levels of management. This ensures the responsibility is assigned to monitor control measures and follow through with processes to flag and fix issues quickly.
2. Open and effective communication
Risk controls stay most effective when processes are well communicated and proper signage is used (in more than one languages if necessary). Additionally, by encouraging open communication, workers will feel more obliged to speak up if problems are noticed.
3. Consultation
Within any PCBU, there are many moving pieces and one person, whether it's a supervisor or manager, can't have eyes everywhere. As a result, there needs to be consultation with workers and HSRs to provide the most accurate insight into how a control measure is working.
4. Up to date training
Control measures often depend on workers having the appropriate knowledge and skill to manage their work safely. This competency should not be assumed, so regular training must be provided to ensure they are capable.
5. Keep updated on potential hazards
Manufacturers, suppliers and/or industry bodies may find new information about hazards, which could trigger a control measure review, or offer more effective controls for existing hazards that could better ensure the safety of your workplace. Therefore, it's important to stay apprised of these updates, so that controls stay relevant and as effective as possible - and if changes are required, they happen before something goes wrong.
Controls are put in place to protect the health and safety of the people in your workplace; however, businesses, projects and technology move at a fast-pace, so those measures can quickly become outdated or less effective. By regularly reviewing your controls and establishing ways of maintaining them, any necessary updates should be made obvious and handled swiftly.
Ready to Learn how RiskWare can help?
Let's organise a time to speak to one of our Risk Specialists and you can learn why millions of users around Australia trust RiskWare to manage their organisations Risks.
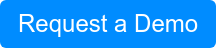
|
If your organisation is looking to improve its workplace health and safety management, software like RiskWare can provide the structure and support you need. Our team always has time for a conversation. Don't hesitate to get in touch!
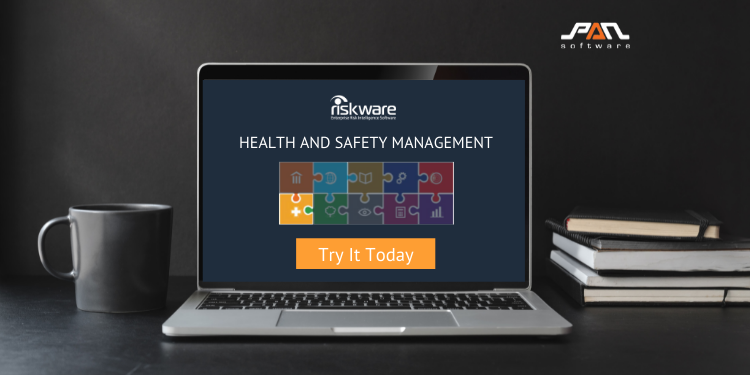
Comments